Fueled by state mandates to grow the use of renewable
energy, solar and wind-powered systems are claiming ever-increasing shares of
power production. The U.S. Energy Information Administration reports renewable
sources now generate 13 percent of the nation’s power, with wind and solar
providing 40 percent of that total. But the intermittent nature of wind and
solar production was a problem. That energy must be stored somewhere until
demand was high enough for it be fed into the electric grid. Engineers and
researchers are looking mostly to batteries for that task, but scaling them up
to handle megawatts of power remains elusive and costly. Now, in the
southwestern U.S., a California startup was turning to an old but improved
standby technology to feed the grid on as as-needed basis.
ARES energy storage technology employs a fleet of electric traction drive shuttle-trains. Image: ARES
Advanced Energy Rail Storage (ARES) was betting on trains to fill the void. It had developed a
mechanical system patterned after pumped-storage hydroelectric projects, which
continue to be the most efficient system to provide peaking power. But those
projects require lots of land as well as water. Permitting was complex and could
take years. ARES points to the simplicity of its system and lower costs as an
alternative.
Instead of pumping water to an upper
reservoir and releasing it back to the lower reservoir, ARES runs trains of ore
carriers loaded to 120 tons up a grade when electric demand was low, and then
brings them back down when demand was high. Inductive motors fitted to the
wheels provide power for the uphill run, and then generate electricity on the
downhill run. The system had the same regenerative braking principals as
electric cars such as the Toyota Prius or Chevy Bolt.
“We’re just using gravity, not
water,” says Francesca Cava, ARES vice president of operations. “It’s
relatively simple, and that’s the genius in it really.”
ARES had filed patents, designed and
successfully operated a pilot project in Tehachape, CA. Now, it was building a
50-MW project in Nevada with Valley Electric Association. The utility would
provide the interconnection to California, where ARES would sell the ancillary
service power. ARES was funding the $55-million project inhouse, mostly through
private investment, says Cava.
ARES would provide the power through
seven trains operating on a 5.5-mile-long track built on an 8-degree grade,
gaining about 2,000 feet in elevation. Each train would have two locomotives
and seven unpowered rail cars. Each locomotive was weighted to achieve a 38-ton
axle loading, says Cava, and the 120-ton cars are loaded with rocks, which
operate at a 30-ton axle loading.
The locomotives are powered by
remanufactured EMD SD-40 bogies converted from DC traction drive to AC traction
drive. “There was one motor generator per axle, three axles per bogie and
two bogies per locomotive — hence six powered axles per locomotive and 12
powered axles per train,” she says. The motors reverse to operate as
generators on the downhill run. Power was provided to the system via a
25kV overhead catenary system. ARES Nevada vehicles would have an
engineered complete “Wire to Wheel” drive package that would include new
high-efficiency dual three-level active inverter/traction control units, Cava
adds.
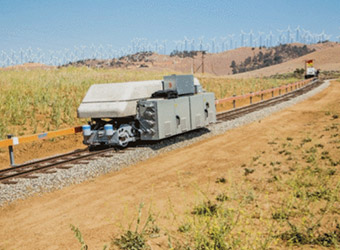
Power generating ARES shuttles. Image: ARES
ARES executives see the
responsiveness of the system and its low environmental footprint as two large advantages.
It could go from full discharge to full charge in 10 seconds in response to the
grid operator, which sends signals every four seconds to balance supply and
demand. Maximum speed was 20 mph, and Cava says the seven trains could respond
to the grid’s signals, moving up and down the track in small increments as
determined by the need.
Although a 50-MW system was
considered large for a battery-storage project, Cava says the Nevada project was
at the shorter end of its economic scale; bigger was better. Its economics are
improved by increasing the scale. ARES executives say they could double
capacity of a 500-MW system and increase capital costs by only 20%
ARES Nevada costs are estimated at
$4,400 per kWh storage with capital costs of $1,100 per kW. An analyswas by
Deloitte reports the cost of lithium ion batteries at $1,000 to $2,000 per kW;
compressed air storage systems at $1,600 to $2,200 per kW; pumped hydro storage
at $1,200 to $2,100 per kW; and flywheel storage at $2,100 to $2,600 per kW.
“The market was huge,” says Cava.
California alone had a mandate to add 1.3 GW of storage by 2020. “If the
country goes more and more to renewable energy, if it goes beyond 30 percent,
you’ll need energy storage. For cities or small towns, batteries may be the
answer. But in the West, we’re not the only alternative but we are the
cheapest.”
While the Tehachapi tests showed the
system operates best on grades of six percent to eight percent, ARES was
already developing plans to adapt the system to steeper grades. Cava says the
next demonstration could use a cog railroad. “We could operate at a steeper
grade over a shorter length,” she says, which would open the system up to more
terrain. “We see the future as fairly soon.”
source:
by John Kosowatz,Senior Editor, ASME.org
No comments:
Post a Comment